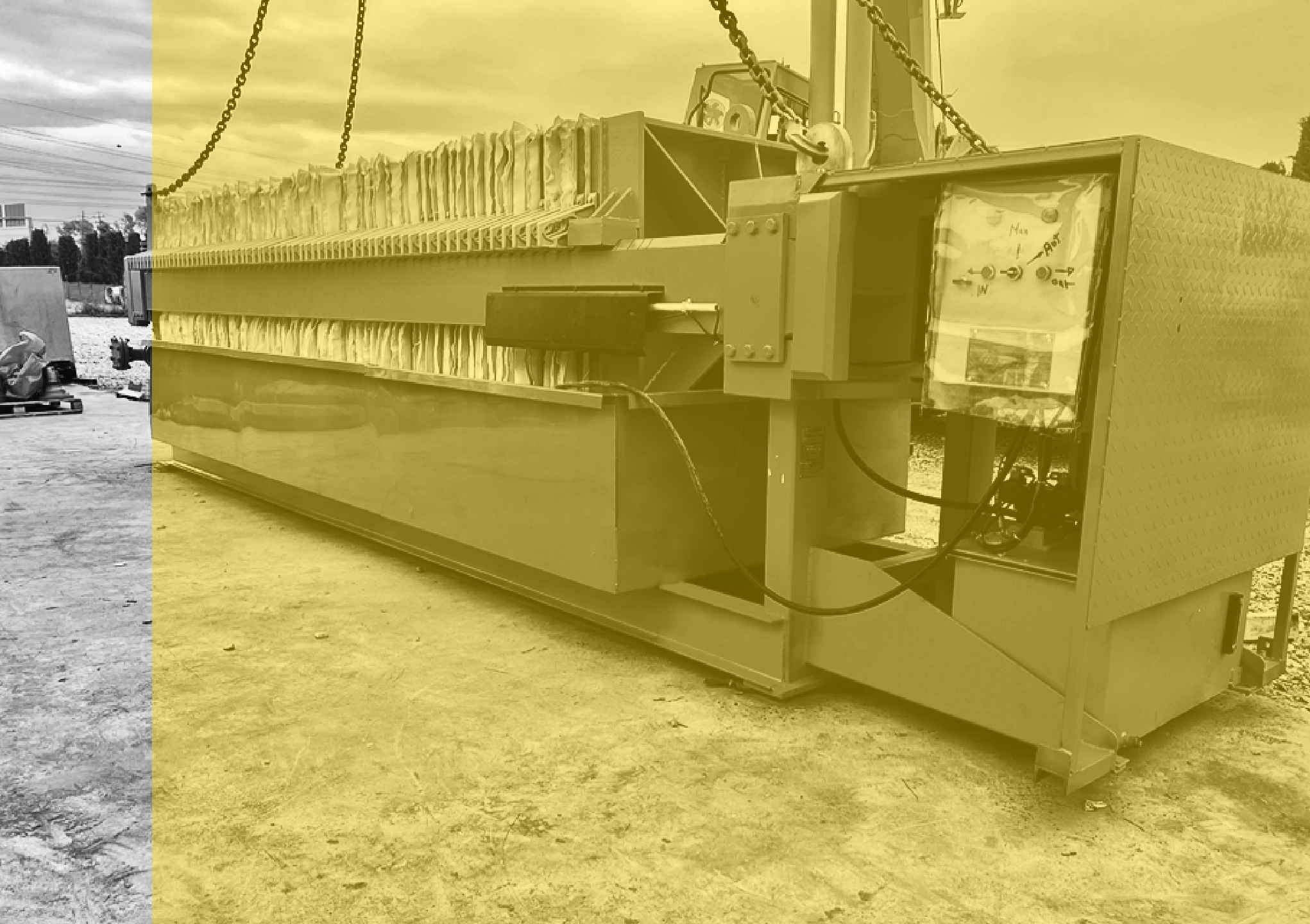

Equipment
Recognizing the significance of efficient solid control systems in drilling operations, Matrix offers a comprehensive range of solid control equipment designed to enhance productivity and minimize waste.
Matrix Drilling Fluids has earned a reputation as a premier provider of comprehensive equipment services for the oil and gas industry. With a strong commitment to innovation and customer satisfaction, the company offers an extensive range of state-of-the-art drilling fluid equipment, specialized tools, and integrated solutions designed to optimize drilling performance, mitigate risks, and enhance operational efficiency.
Cutting-Edge Equipment Fleet
Matrix Drilling Fluids boasts an impressive fleet of cutting-edge equipment, meticulously maintained to the highest industry standards. From centrifuges, shale shakers, and degassers to mud agitators, desanders, and mud hoppers, their equipment lineup caters to a wide array of drilling applications. Each piece of equipment is carefully selected for its performance, durability, and ability to withstand the demanding rig environment.
Customized Solutions
Understanding that no two drilling projects are the same, Matrix Drilling Fluids excels in providing customized equipment solutions. Their team of experienced engineers collaborates closely with clients to analyze drilling requirements and wellbore conditions, tailoring equipment packages that optimize drilling fluid performance. The goal is to ensure seamless integration with the existing rig setup, maximizing efficiency and minimizing downtime.
Rigorous Quality Assurance
Matrix Drilling Fluids maintains rigorous quality assurance practices across its equipment services. All equipment undergoes thorough inspection, testing, and certification to ensure compliance with industry regulations and safety standards. This commitment to quality guarantees reliable and consistent performance of their equipment throughout the drilling process.
Real-Time Monitoring and Support
In today’s fast-paced drilling environment, real-time monitoring and support are critical. Matrix Drilling Fluids’ equipment services incorporate cutting-edge monitoring technologies, enabling remote tracking of equipment performance, maintenance requirements, and potential issues. This data-driven approach empowers drilling teams with timely insights and proactive support, reducing non-productive time and optimizing drilling operations.
Expert Technical Support
Matrix Drilling Fluids sets itself apart with its team of skilled technical experts who provide round-the-clock support to clients. Whether it’s on-site equipment supervision, troubleshooting, or consultation on fluid system optimization, their technical support team is always ready to assist. Clients benefit from the depth of knowledge and experience that Matrix brings to every project, ensuring smooth operations and successful outcomes.
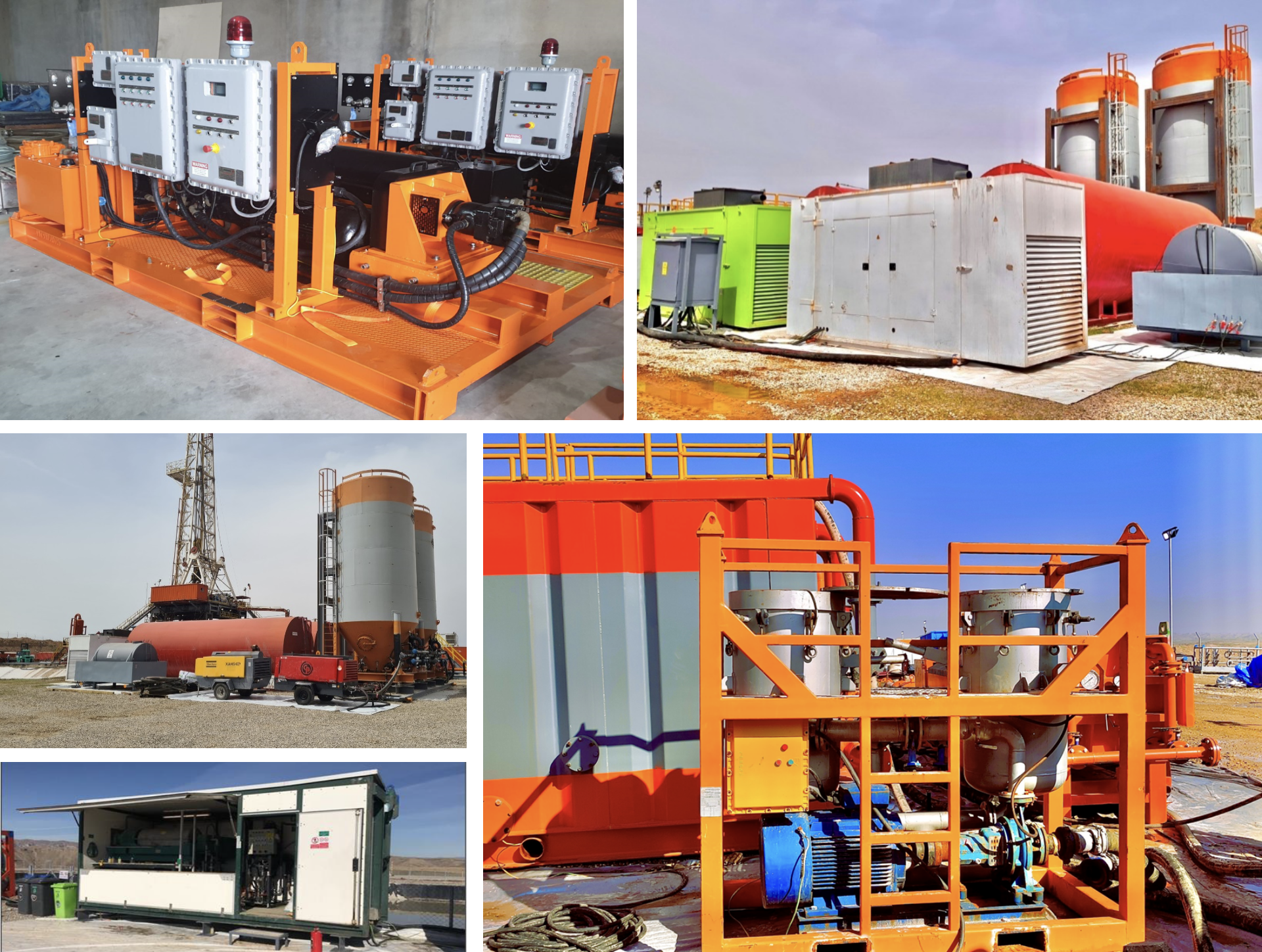

Solid Control Equipment
Decanting Centrifuge:
Matrix drilling fluids have below centrifuges that can be provided to clients as per their special requirements.
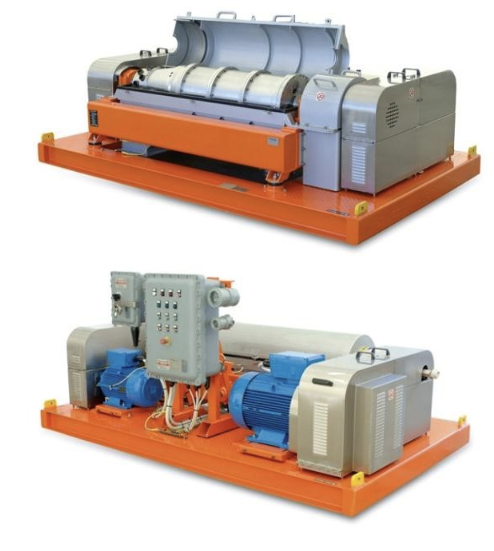
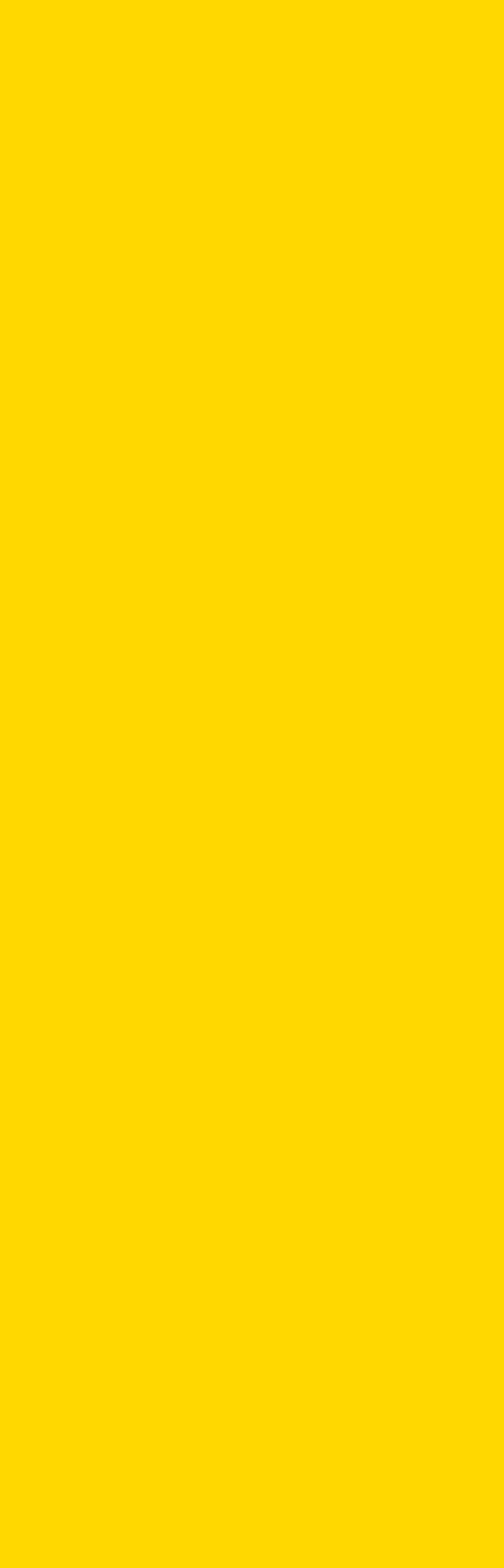
518 VH Centrifuge
Matrix518 HV Centrifuges can remove very fine solids that cannot be removed by any other mechanical separation device.
The discharge restrictions on drilling waste and the incentive of reduced dilution and disposal volumes have made the use of efficiently configured and maintained centrifuges a vital component of the solids control setup.
In un-weighted muds, the centrifuge can greatly improve the separation efficiency of the solids removal system and reduce liquid discharge volumes when used in conjunction with hydrocyclones.
In weighted muds, the centrifuge is used to reclaim barite while removing colloidal drill solids (commercially and technically sensible with weights greater than 11.5 ppg), which can cause high mud viscosity, poor filter cake properties, and decreased penetration rates.

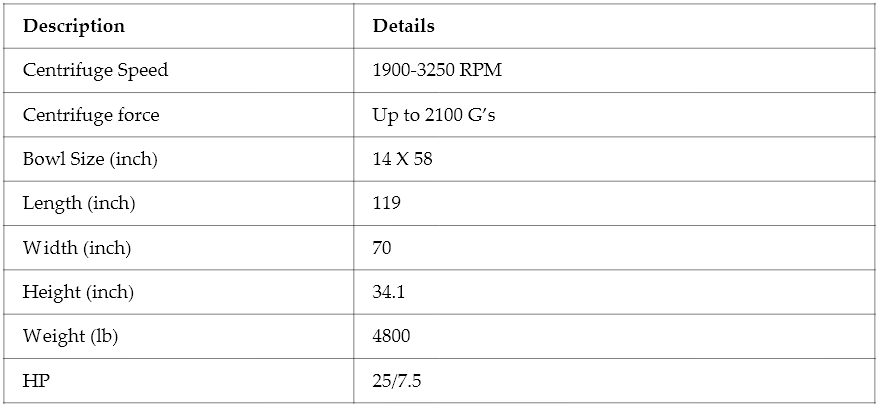
HV FH Centrifuge
Centrifuge is engineered to deliver high performance at low operating costs for both oilfield and industrial applications.
Centrifuges Works in tow mode:
. Solid removal mode: to discard LGS from the drilling fluids.
. Barite recovery mode: recovers 95% of barite and returns it to the active system while rejecting finer, low-gravity solids
HV FH SWACO Centrifuge:
The HV FH centrifuge is designed to handle higher fluid processing rates by providing more power and improving the fluid flow in and out of the machine. Increasing the available power for the main (50 Hp) and back drive (15 Hp) allows more fluid to be fed into the bowl while providing the necessary torque to remove the increased solids load resulting from the higher feed rate.
The unit also has an improved fluid accelerator to reduce turbulence and bring the fluid velocity (both magnitude and direction) up to the bowl’s rotating speed and direction as quickly as possible, reducing the energy consumed for fluid acceleration and reserving more energy for solids conveyance.
Bowl and Scroll material from Stainless Steel.

The best performance indicator for a centrifuge is the cut point, which is the particle size that has a 50% chance of returning to the system in the liquid discharge and a 50% chance of being discarded in the solid discharge, compared to the feed particle size range.

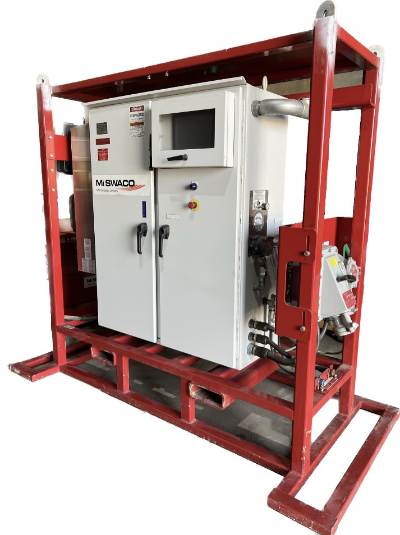
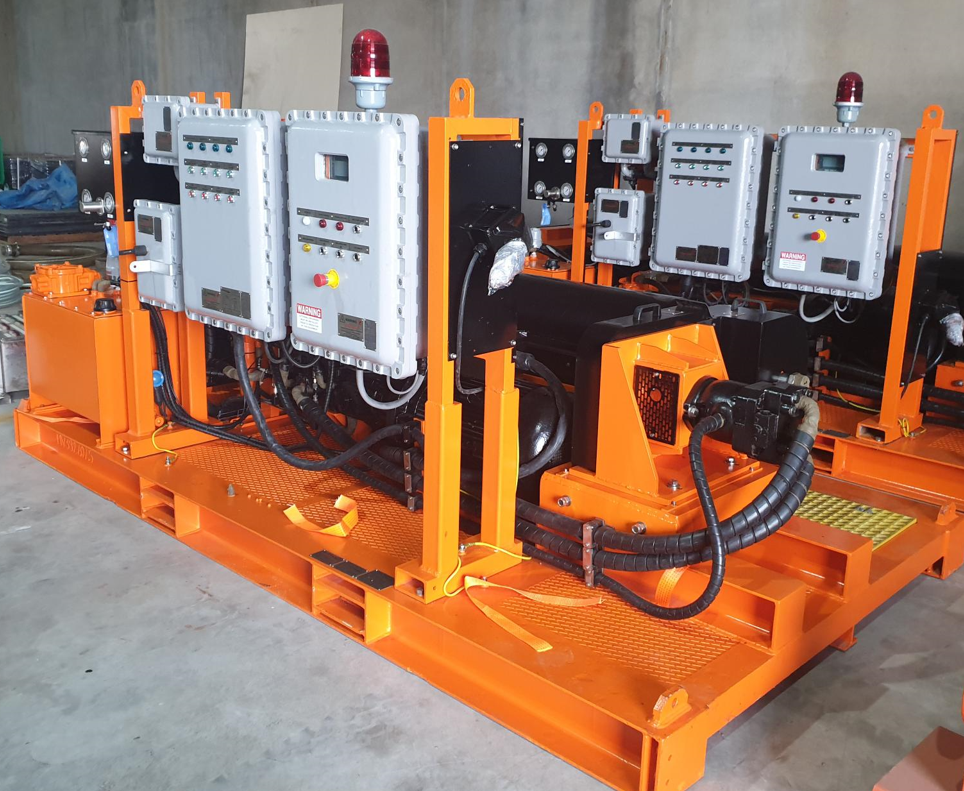
414 Centrifuge
The SWACO 414 Centrifuge delivers high performance and low operating costs for oilfield and industrial mud and fluids handling applications. Decanting centrifuges for fluids cleaning and solids removal and product recovery applications. Ruggedly built for industrial service, they are especially effective in environmentally sensitive areas.
They deliver high recovery rates and efficient solids separation to significantly reduce disposal costs or reclaim valuable material from process streams.
Bowl and Scroll material from Stainless Steel.
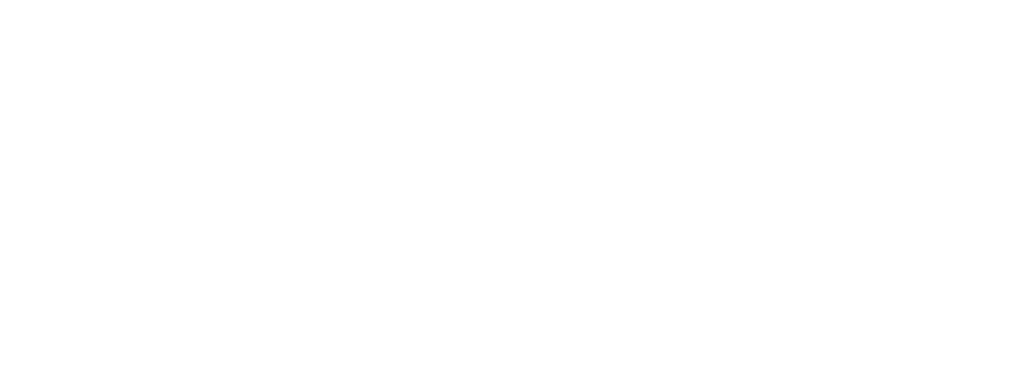

The best performance indicator for a centrifuge is the cut point, which is the particle size that has a 50% chance of returning to the system in the liquid discharge and a 50% chance of being discarded in the solid discharge, compared to the feed particle size range.

Pumps
Matrix is capable of providing feed and Mono pumps beside a wide range of equipment that we can supply to our client.

Feed Pumps
Feed pumps are essential components in various industrial processes, including those that work alongside centrifuges. These pumps are responsible for transferring fluids, such as liquids or slurries, from one part of the process to another. They play a critical role in maintaining a steady flow of material to the centrifuge for separation and processing.
Mono Pump
A mono pump, known as a progressive cavity pump or a single-screw pump, is a type of positive displacement pump that is widely used in various industries for handling viscous, abrasive, and shear-sensitive materials. It is called a mono pump due to its single-screw rotor design, which sets it apart from other pump types. This simple yet effective design makes it well-suited for challenging pumping applications. Matrix drilling fluids posseses an adequate inventory of Mono pumps from well-known brands.
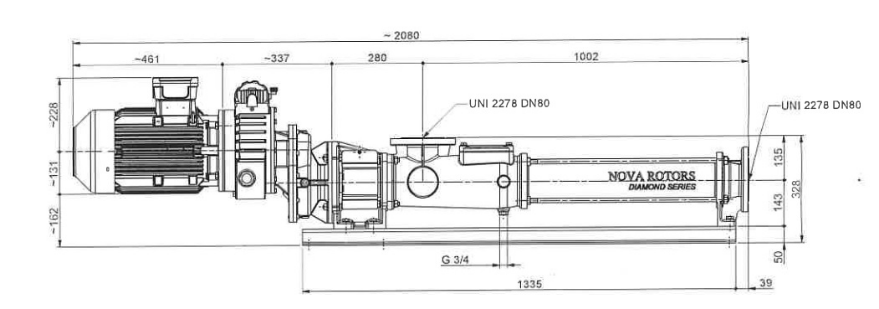
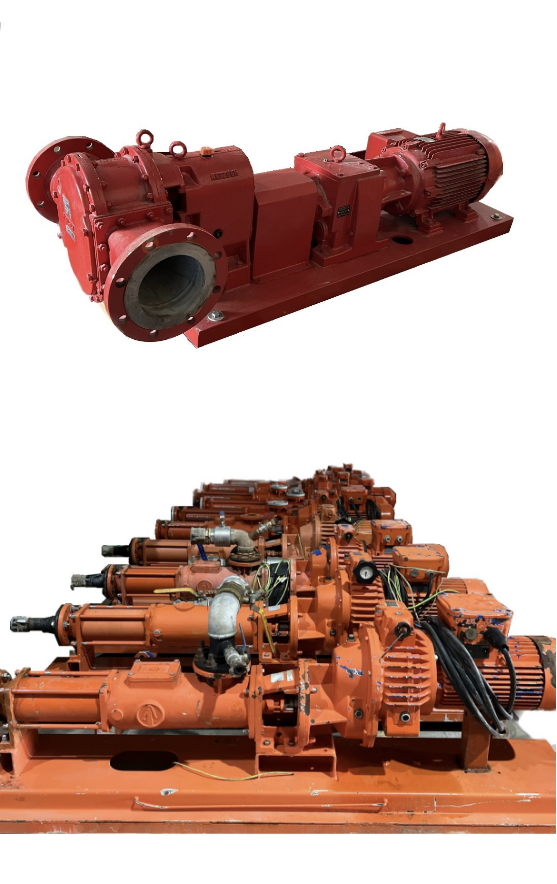
Diesel-Driven Centrifugal Pump
Provides standalone transfer and mixing capability


Shale shaker
Shale shakers are one of the most salient solid control equipment, working as the first line of defense in drilling rigs to remove annoying LGS from the systems. We in Matrix possess various kinds of linear motion shale shakers and we can provide it to our customers as per their entrails.
Specifications of Matrix Shale Shakers:
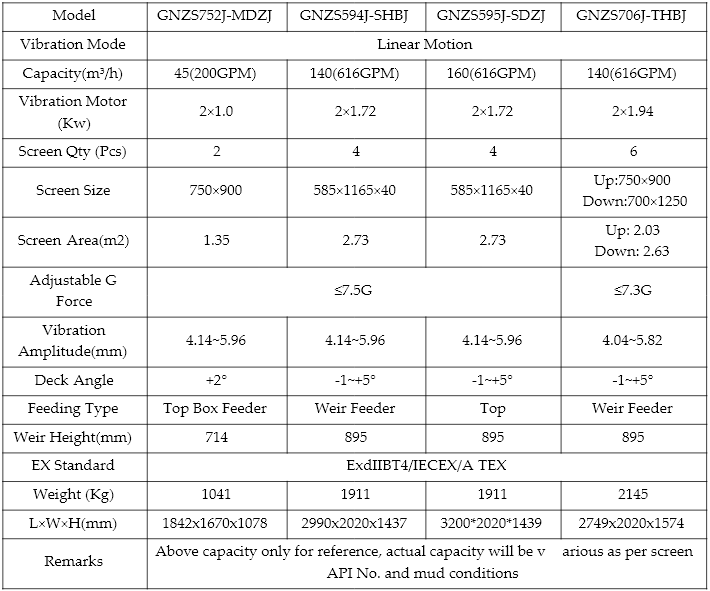
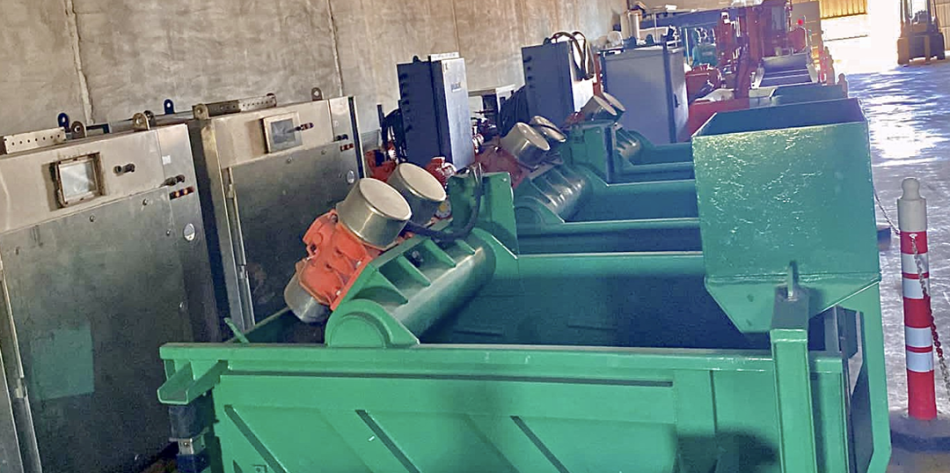
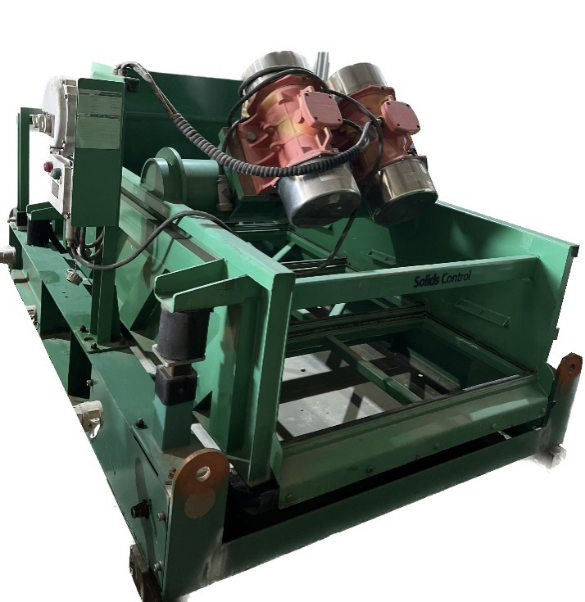
Matrix has the capability to provide shale shaker structure design to modify mud systems and enhance the flow rate capacity of the shale shaker system on oil and gas rigs.
The idea of using extra shale shakers was requested by several clients and it was executed successfully. By adding the below equipment to an existing mud system, the maximum allowable flow rate and handling mud capability on surface holes will be obtained:
. Shale shaker skid
. Shale shaker
. Settling tank
. Transferring pump with floated sensor
. Piping and connection


Mud cleaner
Mud cleaners are designed as highly efficient and cost-effective solid control equipment to remove small size annoying cuttings from the system and enhance drilling operation efficacy in terms of time and cost. This solid control equipment will be located after shale shakers screen on mud system path flow to discard the finer cutting that shakers are not able to take out from the system. This equipment reduces the volume of fluid discard to the waste pit; hence, it saves drilling fluids costs significantly.
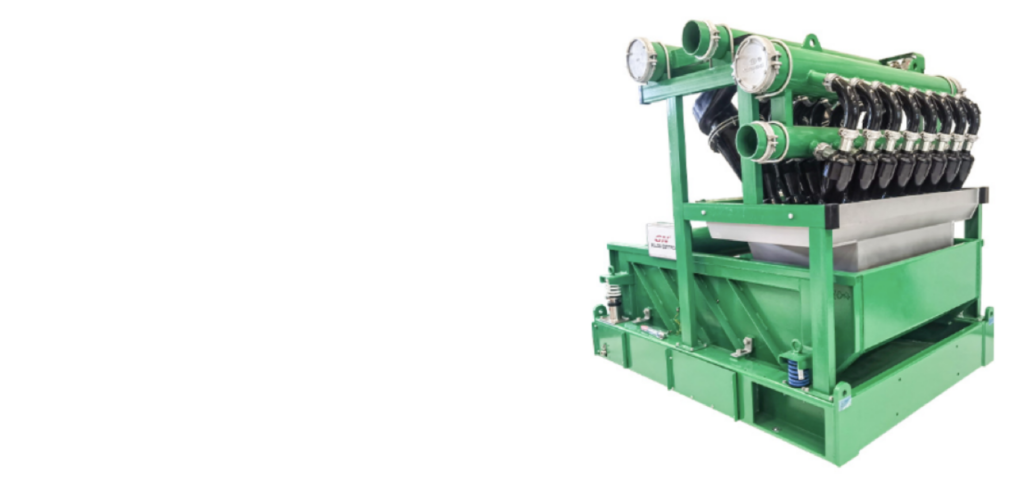

Sumpless drilling equipment
High-G Drying shaker
Matrix Drilling Fluids provides third third-generation linear motion shale shaker and fourth fourth-generation balanced elliptical High-G shaker. Advantages of this kind of shale shaker: high G-force, wide screen area, compressed structure, cost-effectiveness, etc.
Features
Patented shale shaker deck angle adjustable while working, mechanical deck angle adjustment with reliable performance.
Patent tighten rubber sealing for shale shaker deck and screen, long life and easy replacement.
Heat treatment on complete shale shaker deck for High G force operation. Pretensioned shale shaker screen for fast screen replacement
Famous Brand Vibration Motors: IEC Ex, ATEX and UL Certified
Electrical components: SIEMENS, Schneider Brand
Flexible feeding type including Weir Feed, Top Feed, and Hopper Feed for different applications.

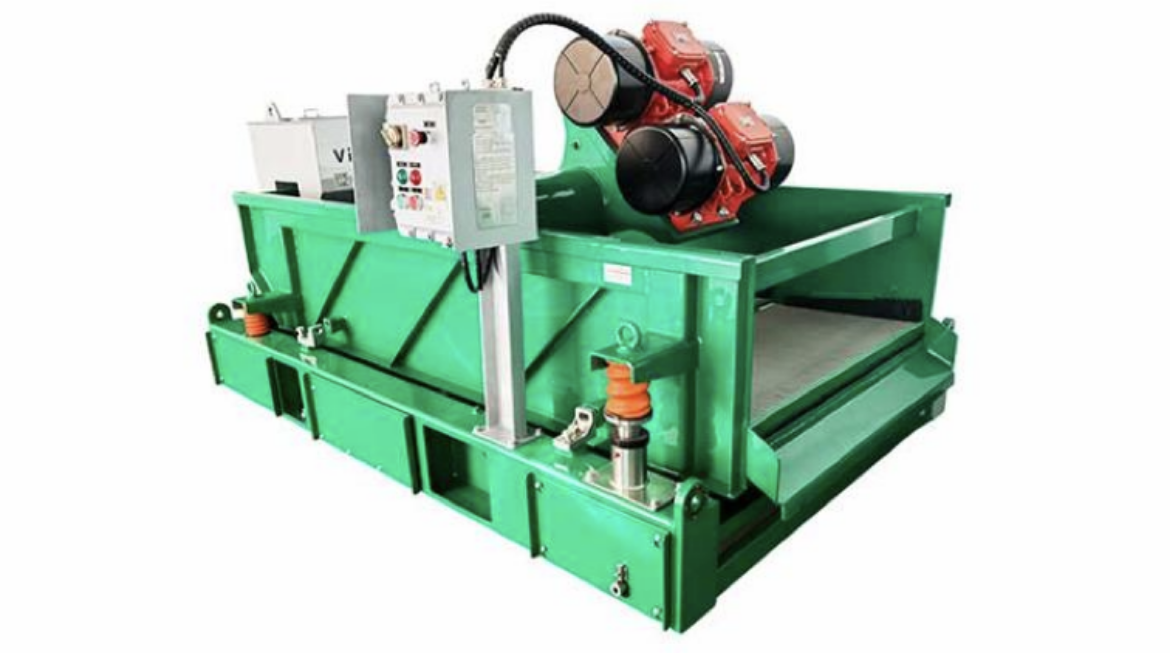
Augers
Matrix Screw Conveyor is used in the oil and gas industry to transfer the drilling cuttings to other solid control equipment or waste pit. Matrix has different sizes of Augers with various lengths to enable customers for different designs.
Features
Reinforced outside frame
Wear resistant coating on screw flights
High-quality bearing seats
Long life-span bearing
Self-lubricating system for inner bearing
Rubbered seal shell cover
Top-quality Motors and gearbox from well-known brands
Emergency stop
Matrix performed many operations in Iraq using augers with a high level of client satisfaction.
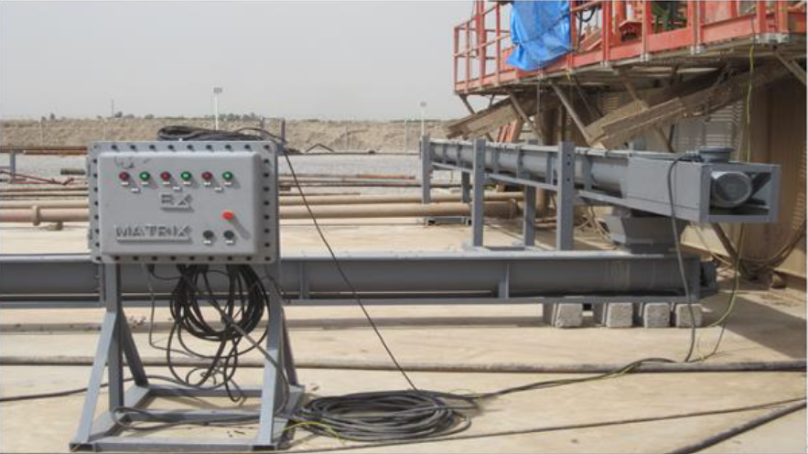
Three-side cutting tank
MATRIX’s 3-sided Tanks are designed with the following features;
Width: Outside 11ft, inside 10 ft
Length: 20ft, 30ft or 40 ft
Inside Height: 3’ 6” (42”), and 5’ 6” (66”)-giving bins of capacity 125 to 392 barrels.
Mounted on two skids, 5ft apart.
Winch Pipe (4”or 5” diameter) on the front and back.
Ramp in the open front.
Cutting skips
We provide the standard closed (sealed) and vacuum-rated cuttings skip with a capacity of 4m3 (25 bbl.) to our clients. Being sealed led this skip to be environmentally friendly as no waste or cutting can be leaked from the top of these skips under any circumstances. The cutting skips can be lifted either by Forklift or crane as per its design.
Matrix performed many operations in Iraq using augers with a high level of client satisfaction.


Filtration
Dual-pod filtration unit
- A dual pod filtration unit, also known as a double pod filtration system, is an advanced and versatile filtration setup used to remove contaminants and impurities from various types of fluids, such as liquids or gases. It consists of two separate filtration pods that work in tandem to provide efficient and reliable filtration.
- Key features and components of a dual pod filtration unit:
- Filtration Pods: The system comprises two separate filtration pods, each containing its own set of filter elements. These pods can function independently or in parallel, depending on the application and the level of filtration required.
- Filter Elements: Each pod is equipped with multiple filter elements, which can be of various types, such as pleated cartridges, depth filters, bag filters, or membrane filters. The choice of filter elements depends on the nature of the contaminants to be removed and the desired filtration efficiency.
- Manifold System: The dual pod filtration unit is equipped with a manifold system that allows for easy control of flow distribution. It enables the fluid to pass through the filter elements in the pods and directs the filtered fluid to the outlet.
- Valves and Controls: The system is equipped with valves and controls that provide flexibility in operation. These allow operators to switch between the filtration pods, isolate individual pods for maintenance, or configure the system to operate with both pods simultaneously for higher flow rates or increased filtration capacity.
Pressure Gauges and Differential Pressure - Monitoring: Pressure gauges are typically installed on the inlet and outlet of each pod to monitor the pressure drop across the filter elements. Differential pressure monitoring helps determine the condition of the filter elements and indicates when they need to be replaced or cleaned.
Advantages of a dual pod filtration unit:
- Increased Filtration Efficiency: Having two pods with separate filter elements enhances the filtration efficiency, ensuring a higher level of contaminant removal and cleaner fluids or gases.
- Continuous Operation: The ability to switch between pods or operate them in parallel allows for continuous filtration even during maintenance activities, reducing downtime.
- Versatility: The unit’s flexibility makes it suitable for a wide range of applications, including industrial processes, water treatment, oil and gas refining, chemical processing, and many others.
- Redundancy: Dual pods offer a level of redundancy. If one pod experiences issues or requires maintenance, the second pod can take over the filtration process, maintaining a continuous flow of filtered fluid or gas.
- Scalability: Dual pod filtration units can be designed with different flow rates and filtration capacities, making them scalable to meet varying process requirements.
- Specification:
- certification: DNV 2.7-1
- Maximum working pressure:7 bar g (100psi)
- Design temperature:70 0 C
- Maximum throughput:172 m3/hour (18 bbl/min) approx.
- Qty of filter elements:50/vessel
- Safety relief valves: One on each vessel
- Cartridgetype:2.7” x 50”
- Tank diameter:24”
- Material: stainless steel
- Pipework configurations:4” Individual / serial / parallel
- Weight (empty):1500 kg
- Dimensions:(W1200mm x L2250mm x H 2250mm)
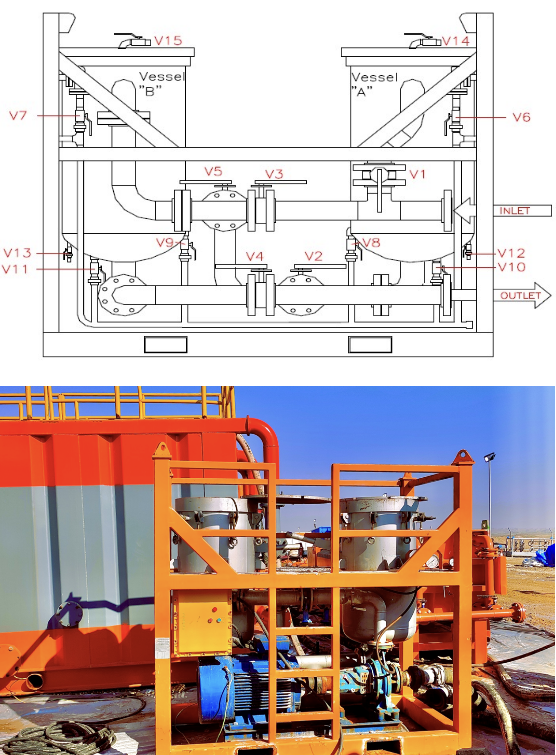
- A DE (diatomaceous earth) filter press, also known as a diatomite filter press, is a type of industrial filtration equipment used for separating solid particles from liquids. It employs the use of diatomaceous earth, a naturally occurring porous material composed of fossilized diatoms, to achieve effective and fine filtration.
- Key components and operation of a DE filter press:
- Filter Press Structure: A DE filter press consists of a series of vertical plates arranged alternately with frames. The plates are typically made of polypropylene, cast iron, or stainless steel, and they are covered with filter cloths. The frames hold the plates together, creating a series of chambers.
- Diatomaceous Earth (DE) Pre-coat: Before starting the filtration process, a thin layer of diatomaceous earth is pre-coated onto the filter cloths. This pre-coat forms a porous and permeable medium that will trap and retain the solid particles during filtration.
- Filtration Process: The process begins by pumping the liquid mixture, which contains the suspended solid particles, into the filter press. The liquid passes through the pre-coated filter cloths and diatomaceous earth, leaving behind the solid particles that are trapped in the DE layer.
- Cake Formation: As the filtration progresses, the solid particles accumulate on the filter cloth and form a layer known as the filter cake. This cake helps to enhance the filtration efficiency and provides a platform for further solid particle removal.
- Cake Drying and Discharge: Once the filtration is complete, the filtered liquid, now free of solid particles, is collected and discharged from the press. The dry filter cake can be removed from the filter press and discarded or processed further, depending on the application.
- Advantages of DE filter presses:
- High Filtration Efficiency: DE filter presses offer excellent filtration efficiency, capable of removing fine particles and achieving high clarity in the filtrate.
- Versatility: DE filter presses are versatile and can handle a wide range of materials, making them suitable for applications in industries such as food and beverage, pharmaceuticals, chemicals, and wastewater treatment.
- Easy Cleaning and Maintenance: Cleaning and maintaining a DE filter press are relatively straightforward. The filter cloths and DE layer can be easily replaced, ensuring consistent and reliable filtration performance.
- Cost-Effective: The use of diatomaceous earth as the filtration medium can be cost-effective, especially when dealing with large volumes of liquid containing a high concentration of solid particles.
- Sustainable and Environmentally Friendly: Diatomaceous earth is a natural and renewable resource, making DE filter presses an environmentally friendly filtration option.
Here in Matrix, we have De-filter press and we are providing it to our client along with De-Powder which is the main product using for filtration job with this equipment.

Waste management equipment
Oil Sludge Treatment Plant
- An oil sludge treatment plant is a specialized facility designed to efficiently and effectively process large quantities of oil sludge. Oil sludge is a complex mixture of oil, water, and solid particles that accumulates as a byproduct of various oil-related processes, such as oil drilling, refining, storage tank cleaning, and oil spill cleanups.
- The main purpose of an oil sludge treatment plant is to separate the different components of the sludge, recover valuable resources, and properly manage the waste materials. The treatment process typically involves several stages to ensure thorough and safe processing of the oil sludge.
- Key components and processes in Matrix oil sludge treatment plant:
- Sludge Reception and Pre-Treatment: The oil sludge is received and stored in the plant. During pre-treatment, large solid objects and debris are removed, and the sludge is conditioned to improve its processing characteristics.
- Centrifugation or Decantation: The primary separation process involves using centrifuges or decanters to separate the sludge into its three main components: oil, water, and solid particles. The centrifugal force separates the phases based on their densities.
- Oil Recovery: The recovered oil is further processed to remove any remaining impurities and contaminants. It can be reused or sold as a valuable product.
- Water Treatment: The separated water, which may contain some residual oil and other contaminants, undergoes additional treatment to remove impurities before safe discharge or reuse.
- Solid Waste Management: The solid residues left after centrifugation or decantation are usually considered waste and need proper disposal or further treatment. This may involve sending the solid waste to a landfill, incineration, or sending to Asphalt factories.
- Wastewater Management: Any wastewater generated during the treatment process is properly managed and treated to meet environmental regulations before discharge.
- Environmental Compliance: Adherence to environmental regulations and guidelines is crucial to ensure that the treatment operations do not harm the environment or pose any health risks.
- Recycling and Resource Recovery: Some components of the oil sludge may be suitable for recycling or further processing into valuable products, such as re-refining recovered oil or converting solid residues into usable materials.
We in Matrix executed oil sludge treatment projects in different locations all around Iraq with our quality equipment and facilities. We are ready to take the lead for oil sludge treatment plan as part of our waste management operations.

Dewatering unit
- Dewatering Systems have become common practice and an industry-standard in “closed loop” systems to achieve zero discharge operations, especially in environmentally sensitive areas using water-based muds.
- Displaced or excess drilling mud, along with the excess location liquids produced on location are transferred into a storage tank and sampled prior to Dewatering. The dewatering system is utilized to process the liquid waste from the active mud and or storage tanks.
- The cleaned effluent from the dewatering system can then be:
- returned to the active mud system, as dilution
- returned to the drill water tanks
- Treated further to acceptable regulatory discharge standards for release to the environment
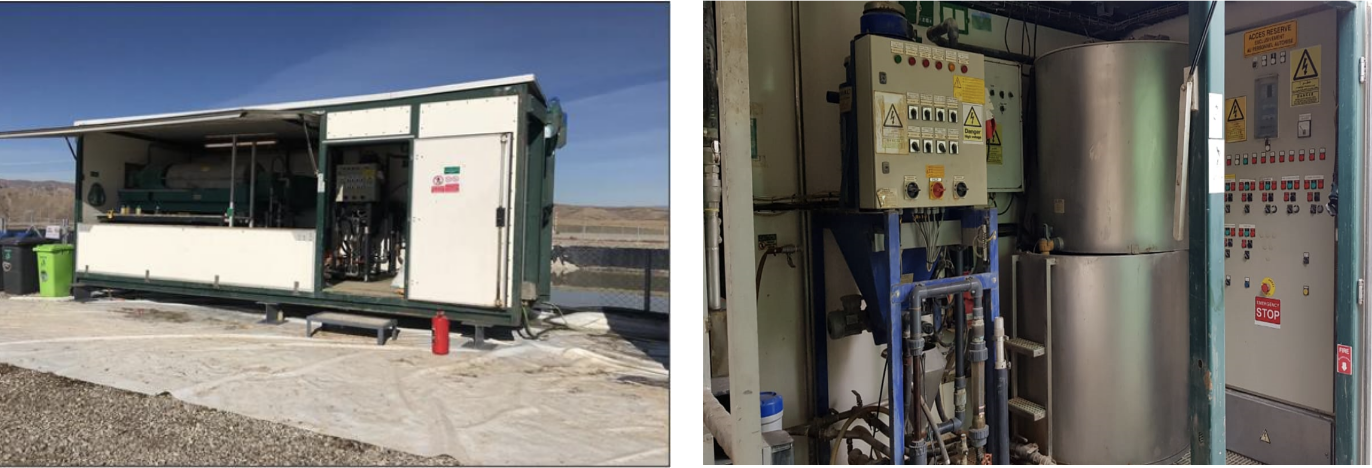
Evaporator (Atomizer TYEME EOLO 3100)
Fluid evaporation is widely used when dealing with important fluid volumes. Fluids that were accumulated for a considerable amount of time and separated by gravitational effect from solids need to have certain consistency for further processing purposes, therefore water evaporation will increase volumes processing per day hence allowing for safe, environmentally friendly processing of the solid’s component in the aqueous suspension.
The advantageous use of a fluids evaporation system is evident on economic factors also, for example cutting down waste-handling costs associated with drilling sites remediation activities.
The only negative side of evaporation system utilization could be regarded the duration of this process, which normally exceeds the duration of waste transportation for disposal.
After a careful project budgeting, the comparison between fluids evaporation and transport processes will lead to the conclusion that, even though fluids evaporation process will demand additional costs, it does not exceed transportation fees for the same volumes processed
The rear deflector 11 static blades stainless steel provides radical air turbulence and distribution 50% to 750%. The aerodynamic diameter nozzle co 1,015 x 500 mm is made of stainless steel and has 4 channels. The system channels air increases production by 17% thereby preventing the upper fast air collide with the slow in the central area. adjustable air output ranging from 22m / sec to 44 m / sec.
The lower channel -TURBO- gets no extra consumption by 16.50% of the air is wasted in other atomizers. The chassis is very robust (Combi System) S2 steel. Subframe in middle of the tank, standard on 3000 l. It has extendable and adjustable throw six positions, bumper protector group air, metal kickstand wheel, and extendable footrest. Shells are made of polyethylene uniform.
These groups have 3 levels of air getting mixed homogeneous mixture constant and high, medium and low pressure, and a total sweep background.
The model Eolo GTO10 3100 has dimensions of 4,767 x 1,800 x 1,825 mm and 1,256 kg tare.
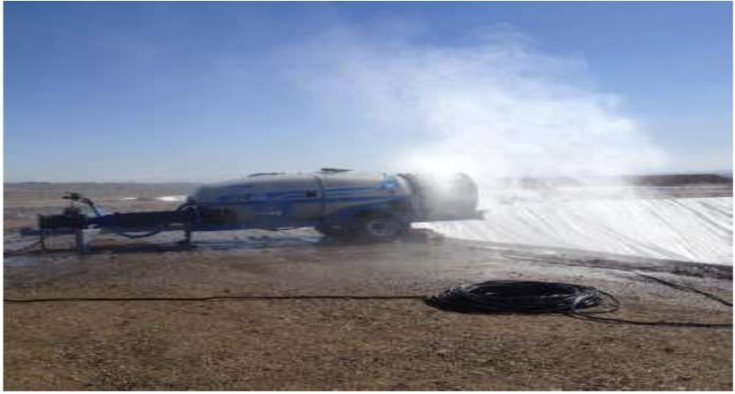
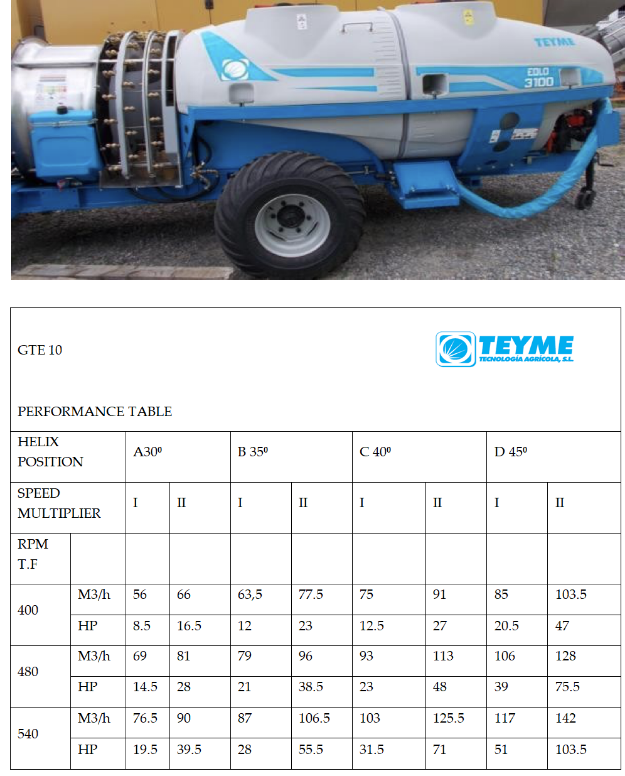
Boiler
In waste management jobs on oil fields, boilers play a crucial role in the treatment and disposal of various waste materials generated during oil drilling and production processes.
Purpose: Boilers are used to treat and process various types of waste generated on oil fields, including drilling mud, cuttings, produced water, and other liquid and solid wastes.
Produced Water Treatment: Produced water is water that comes to the surface along with oil during extraction. It contains impurities, hydrocarbons, and other contaminants. Boilers are employed to treat produced water, separating oil and other pollutants, making it suitable for reuse or safe disposal.
Environmental Compliance: Waste management on oil fields is subject to strict environmental regulations. Boilers used for waste treatment must meet these regulatory standards to ensure safe and environmentally responsible waste disposal practices.
Safety Considerations: Boilers involve high temperatures and pressure, and safety is of utmost importance. Proper training, maintenance, and safety protocols are essential to prevent accidents and protect workers on the oil field.
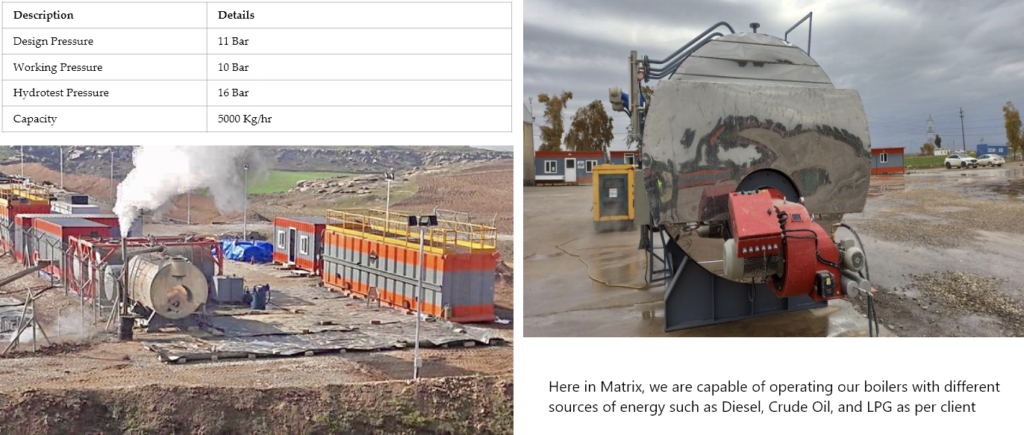
Oil Skimmer
The Skimmer is a portable unit for quick response to small spills from light to medium viscosity oils in harbors, lakes, and rivers. Suitable for both advancing and stationary skimming operations, and due to its shallow draught allows skimming close to shorelines and in shallow waters. Also, suitable, without its three pontoons, for fixed installation in API-tanks, pits etc.
Equipped with the well proven self- adjusting flow-controlled inlet weir.
Always parallel to surface!
Automatic compensation for waves and swell.
Light weight and easy to use.
Can be used with any type of vacuum pump with capacities up to 30 m3/h.
(Capacity Up to 30 m3/h (135 gpm), depending on available pump capacity)
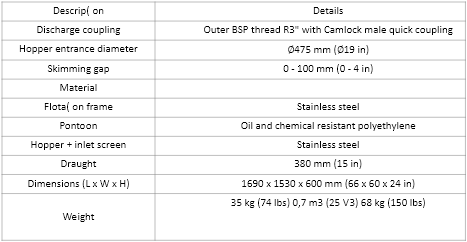
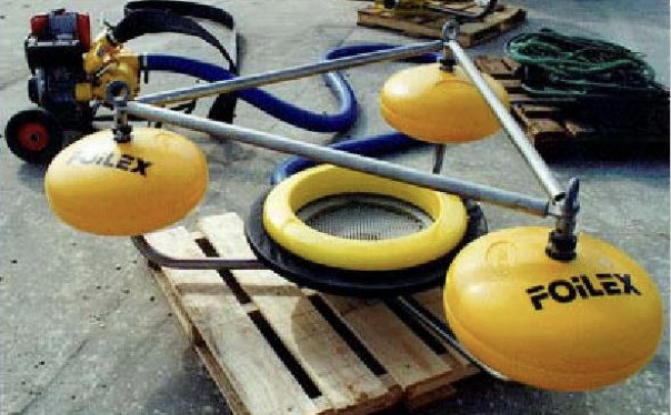
Super Vacuum Pumps
The SX280-V is a high volume, heavy duty vacuum pump, capable of capturing high density slurries via a strong 25”Hg vacuum combined with high volume airflows.
The SX280-V can handle solids to 80% of the employed hose diameter and will transfer up to 30 m3/hr + depending on the materials and distances involved.
The SX280-V has no moving components that come in contact with the material being pumped and can pass rags, bolts and many other items that would render a standard impeller pump, inoperable.
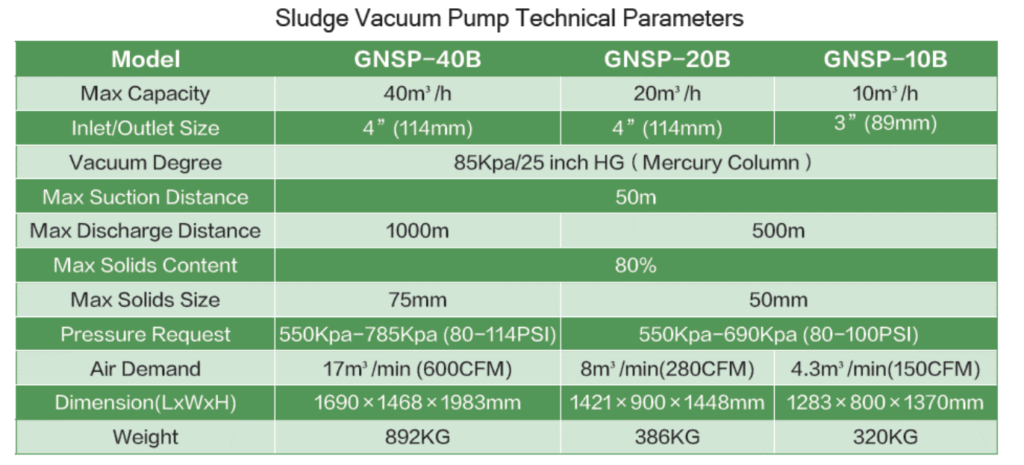
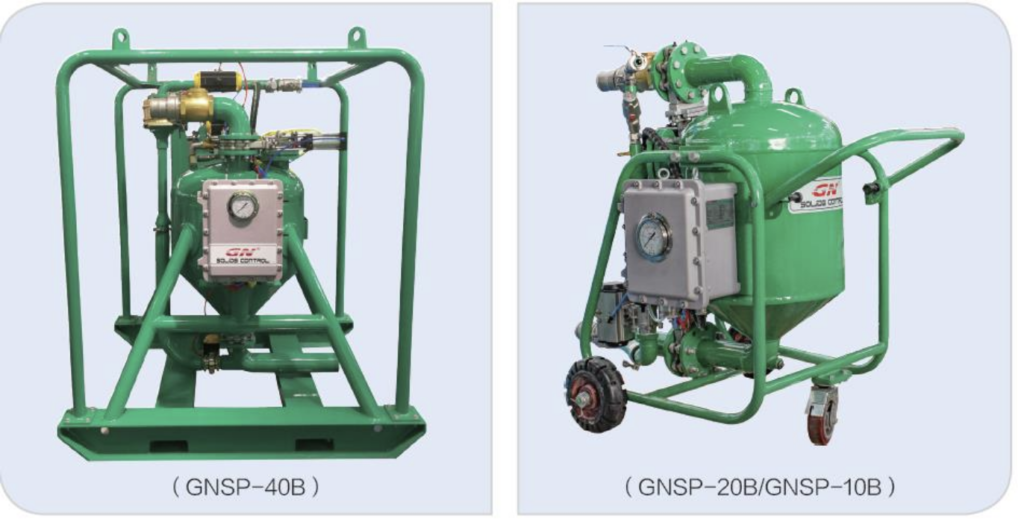
Features:
100% compressed air operation
Intrinsically safe
Fixed or mobile
Manual or fully automatic
Robust construction and low wear characteristics
Delivers up to 1000 meters (1094 yards) horizontally and 35 meters (38 yards) vertically
High vacuum 24”Hg+ and high airflow
High solids content (80%+) transfer
Applications:
Spillage recovery and transfer
Sump cleaning and desilting
Tank Bottoms and sludge extraction
Pneumatic excavation and dewatering
OBM transfer and pit cleaning
Bentonite, sand, and cement powders transfer
Technical Data:
Height 557mm (62”)
Width 1400mm (55”)
Length 1355mm (53”)
Weight 720kgs (1584lbs)
Air consumption 600cfm at 85psi+
25’hg+ (85kPa) vacuum
Suction inlet 75mm (3”)
Discharge outlet 100mm (4”)
Handles solids to 75mm (3”)
The Solids Pumps utilize high airflow and vacuum (up to 85kPa vacuum at 700kPa air pressure) to ensure high performance. The SX Solids Pumps are designed to convey recovered material under pressure through a pipeline or into a collection vessel. Alternatively, deadheads and cuttings carousels are available which absorb and dissipate the discharge pressure and allow the delivery of material under gravity to a confined location such as a conveyor belt or cuttings skip.
Two modes of positive pressure discharge are used in SX Solids Pumps; dense phase and lean phase pneumatic conveying. The latter can achieve vertical heads in excess of 35 meters (115ft) and horizontal discharge distances of over 1000 meters (3280ft).
The absence of any electrical supply in SX Solids Pumps makes them useful in restricted or potentially hazardous areas.
Zero Discharge
The Zero Discharge of drilling waste handling system designed to recover liquid waste volumes and maximize removal of unwanted drill solids in accordance with client environmental regulations:
- Eliminate Dump & Dilute waste volumes (Closed Loop)
- Eliminate waster volumes from flushing cuttings.
- Minimize solids waste volume.
- Capture any whole mud losses from the shakers.
- Maintain low % LGS in the circulating system and lower treatment costs.
- Dispose drill cuttings to approved disposal area.
- Reduced Operating costs
Matrix has full setup for sumpless operation as per below list: - Augers/ Screw Conveyors System
- Decanting centrifuges with Barite recovery system
- Dewatering system
- High G Drying Shaker
- Cuttings collection Tanks (Halfmoon Tanks)
- Three sided tanks
- Cuttings Skips
- Transfer Pumps
- Sludge Pumps / SUPA VAC Pumps
- Fluids Storing Tanks
- Power Generators
- Screens and spare parts for solids control and waste management equipment
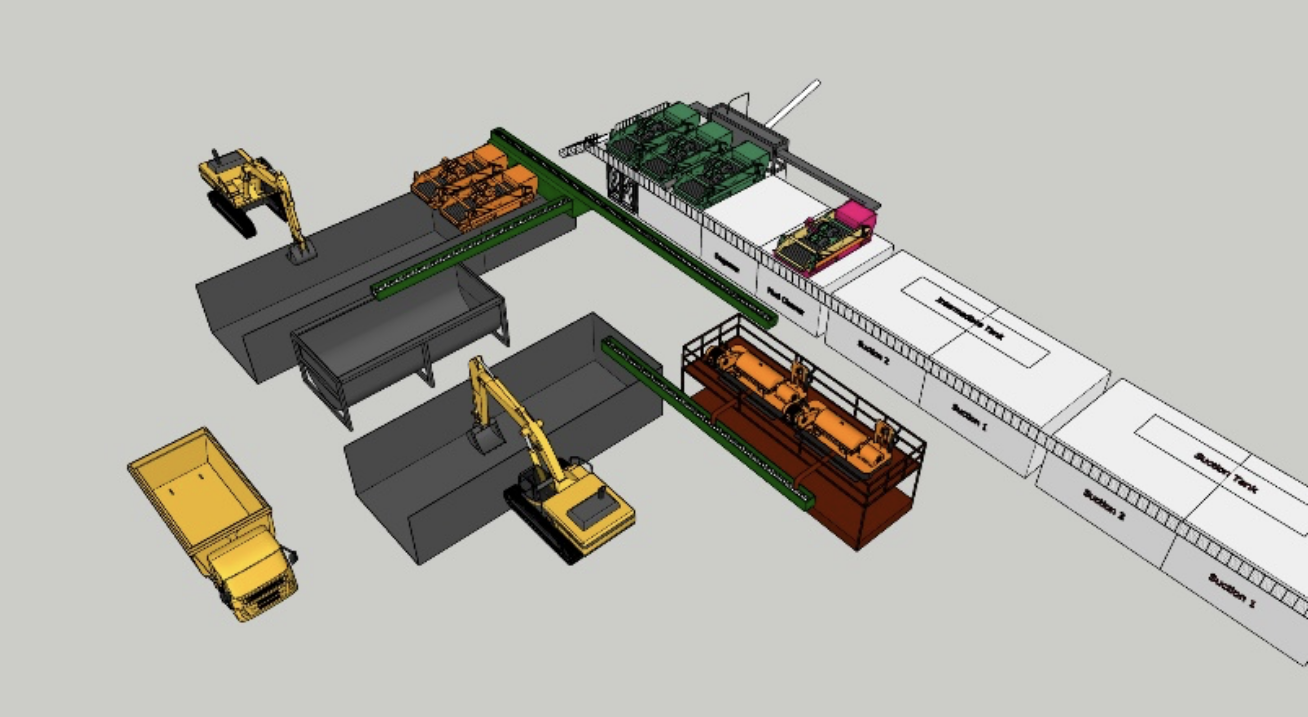
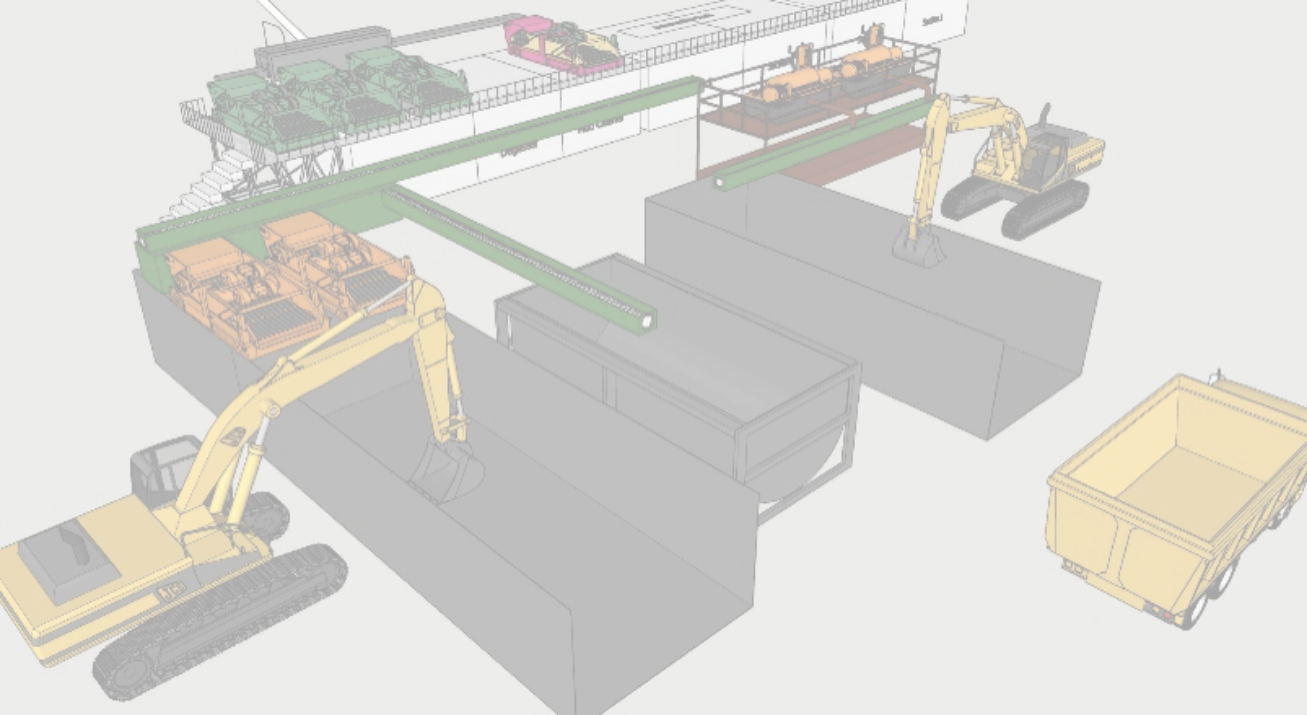
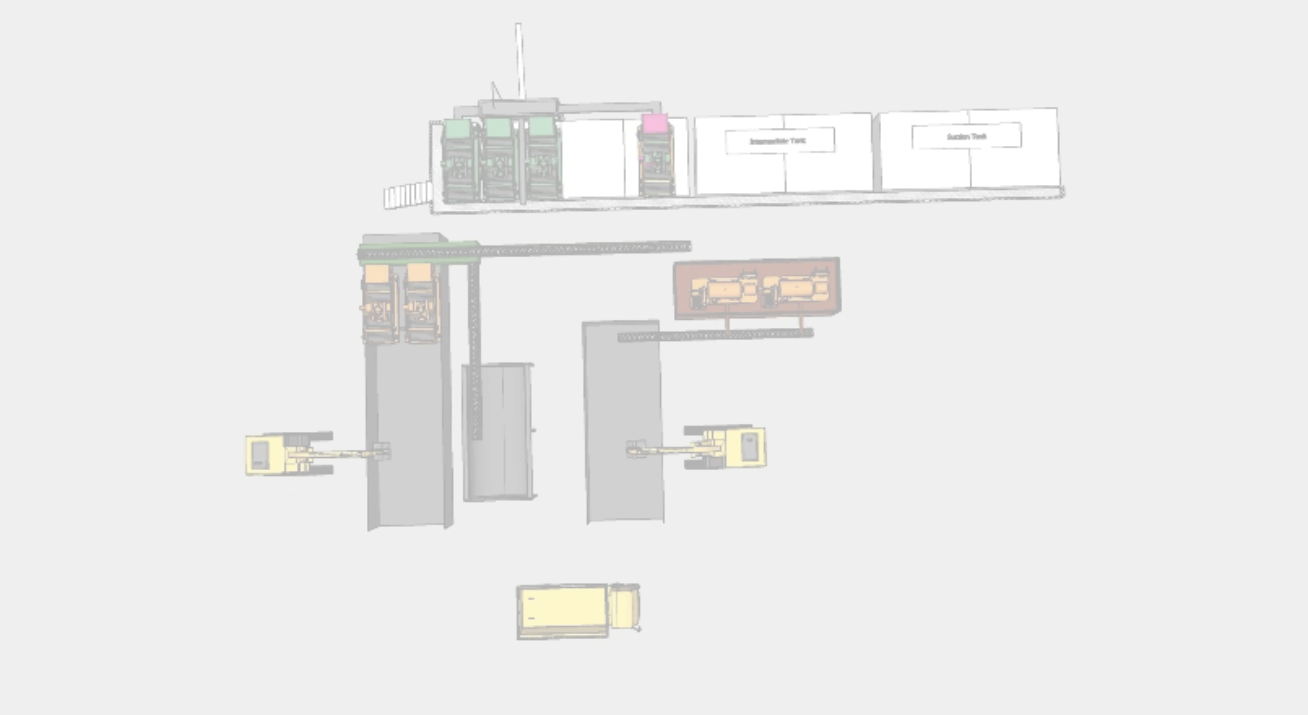

Mud plant
A mud plant, also known as a drilling fluid plant or mud mixing plant, is a crucial facility in the oil and gas drilling industry. It plays a central role in the drilling process by providing and maintaining drilling fluids. We as a drilling fluids and waste management company possess a wide range of equipment and we are able to design and rig up desired mud plants as per our client’s requirements.
Mud plants consist of different equipment for the end of storing and providing drilling fluids in the oil and gas industry. Here at Matrix, we are providing all of this equipment solely or as a package and we are ready to provide it to our client as per their requirement.
Mud tank
- 500 bbls. mixing tank with agitators are using to store mud as reserve tank as well as Active mud tank in mud systems. Each tank has 3 agitators to provide proper mud shearing and avoid settling of inert materials on bottom of the mud tank.
- Special engineering points are considered in designing Matrix tanks which made this mud tanks non-identical to mud tanks in oil and gas industry. Some of these points are as below:
- Proper suction line design inside the tank to minimize dead volume to almost zero.
- Mud guns are located in 3 different places inside the tank.
- 3 powerful mud agitators are located on these mud tanks.
- Quality valves are being used to avoid any leakage in the mud system including more than one tank.
- Flash jet are designed at bottom of the tanks to ensure no sediments will remains on the bottom.
- Three dump valves at the bottom of the tank for better cleaning.
Lobster Shear Hoppe
The Matrix Lobster Mud Hopper is a high-performance uniquely designed to operate in demanding slurry mixing jobs. Handling high flow rate requirements, high solids content, and difficult-to-mix additives are major criteria for meeting demanding slurry mixing conditions in applications such as oil and gas drilling fluid mixing, construction material production, chemical production, mining, liquid sugar mixing, brine mixing, paint pigment mixing, metal processing, and plastic production. Shear hopper will connect to a centrifugal pump, which provide high flow mud passing through the discharge line from pump, where the air suction created by the fast-paced moving mud in hopper nozzles, make any chemical easy to enter and mix inside the drilling fluids. Matrix providing shear hopper from well-known manufacturers.
Matrix lobster shear hopper are compatible to be used in bulk system.
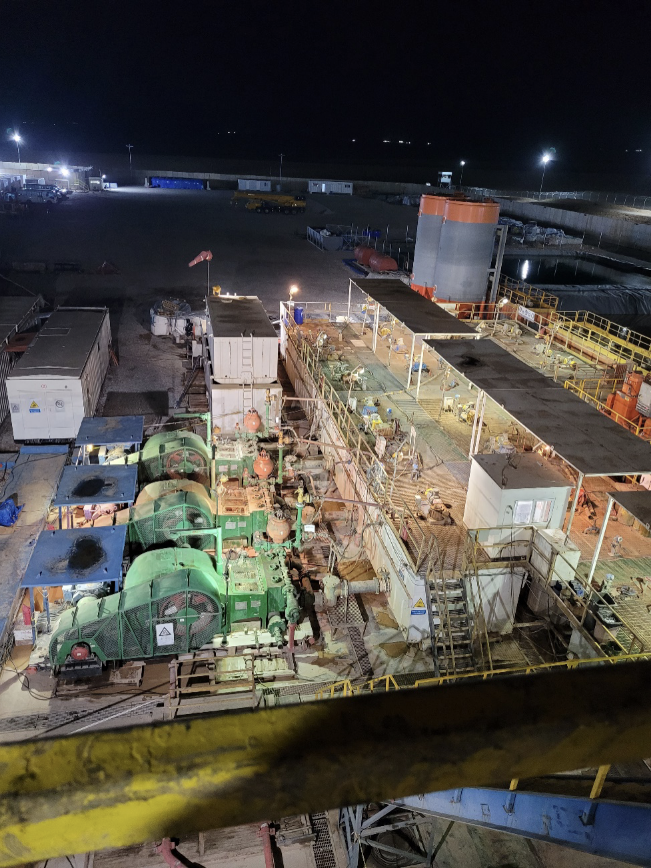
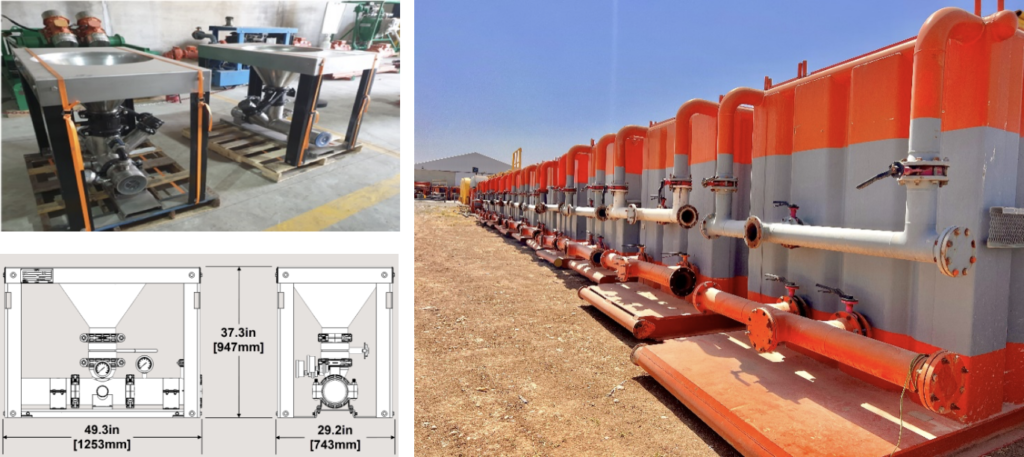
Mud Gun
Mud Guns are part of mud plant and assembling inside the mud tank. As per source of pressure which can be centrifugal pump, or mud pump, or the shear pump, mud guns are classified to three categories of Low, Medium, and high pressure. At the end of the mud guns, special jets are located which create required hydraulic power to create turbulent flow at the bottom of the tank and shear the mud properly.
Matrix facilitates its mud tanks with guns lines to improve the efficiency of the tanks and reduce the time of tank cleaning, minimize dump and dilution of the mud, which finally will lead to cost saving.

Agitators
Mud tank agitators are essential components in a mud plant or a drilling rig used in the oil and gas industry. They play a crucial role in the proper mixing and agitation of drilling fluids, also known as mud. The agitation process is essential to prevent the settling of solid particles and maintain the desired properties of the drilling fluid for efficient drilling operations.
Key features and functions of mud tank agitators:
Agitation and Mixing: Mud tank agitators are designed to agitate and mix the drilling fluid inside the mud tanks. They prevent the formation of a stagnant layer at the bottom of the tank, ensuring that the drilling fluid remains well-mixed and homogenized.
Preventing Settling: As drilling fluid sits in the mud tanks, solid particles such as drill cuttings tend to settle to the bottom due to gravity. Mud tank agitators keep the drilling fluid in motion, preventing the settling of these solid particles and maintaining a consistent density and viscosity of the mud.
Homogenization: The agitation process helps in uniformly dispersing and mixing various additives, chemicals, and weighting materials in the drilling fluid, ensuring that the entire mud volume has the desired properties.
Solids Suspension: Mud tank agitators help suspend the solid particles evenly throughout the drilling fluid, allowing for efficient removal of cuttings using solids control equipment like shale shakers, desanders, and desilters.
Matrix Providing wide range of mud agitators on the mud tanks as per the capacity of the tank and the drilling fluids that is planned to be used. Mud weight, fluid rheology, and many other parameters have pivotal effect on selecting proper agitator. Below are the agitators that we are providing in our mud plants.

Bulk Silo
Matrix bulk silos are using to store bulk materials such as CaCO3, Barite, Hematite, etc. in huge amount. These silos have different capacity which can be selected as per client’s request. Bulk silos are main components of Bulk systems which are using in the oil and gas rigs to mix mentioned materials inside the drilling fluids promptly. Average speed of pumping materials in to the system is 1.5 to 2 MT per minute. The advantages of using bulk systems are as below:
- Saving mixing time
- Quality mixing and consistent mud parameters
- Minimizing material spill on the location
- Increase rig space efficiency
- Improve drilling performance
The bulk silos that we have in Matrix drilling fluids have below appealing aspects:
- Precise weight indicators
- PSVs from well-known manufacturers
- Self-located vertical and horizontal skid
- Easy access for fill, vent, and discharge line
- Manhole on bottom of the tank for easier cleaning
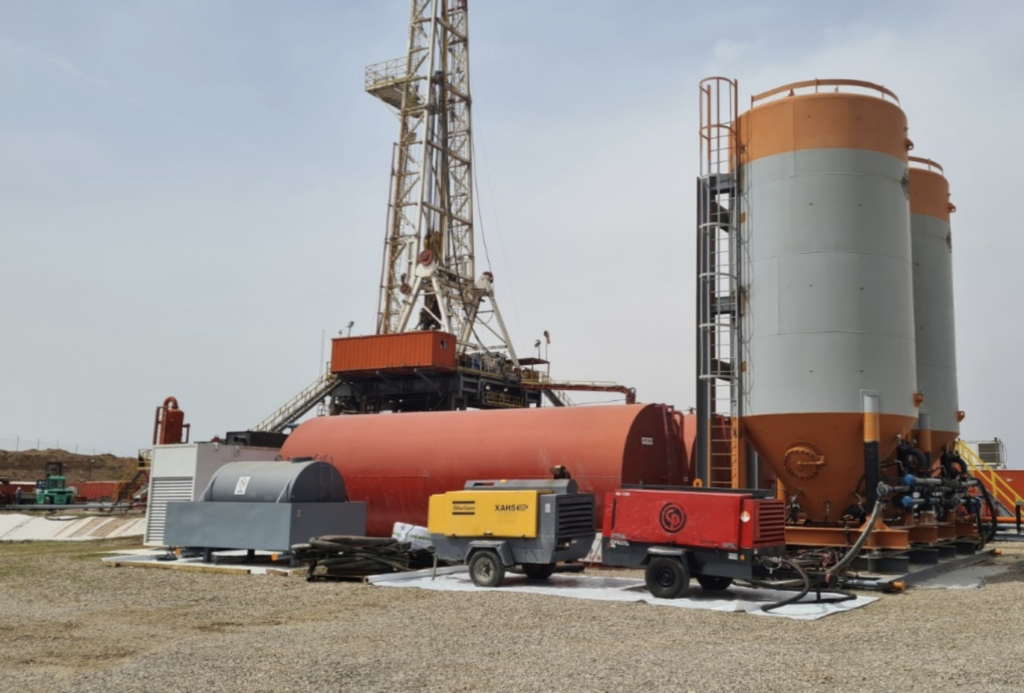
